Accurate recordkeeping under the Occupational Safety and Health Administration (OSHA) can help ensure that your organization operates lawfully and ethically.
Beyond protecting businesses from financial penalties, meticulous adherence to OSHA’s standards under 29 CFR 1904 embeds workplace accountability and employee safety into an organization’s culture. This blog explores the nuances of OSHA regulations so you can avoid common but costly mistakes.
For context, OSHA logs are part of the injury and illness recordkeeping requirements outlined in 29 CFR 1904. They primarily include the OSHA 300 log (Log of Work-Related Injuries and Illnesses), the OSHA 301 form (Incident Report), and the OSHA 300A form (Summary of Work-Related Injuries and Illnesses). Improperly completed OSHA logs can result in citations, fines, and devastating reputational damage—regardless of your industry.
Most Common Errors in OSHA Recordkeeping (and How to Avoid Them)
1. Misclassifying Work-Related Cases
The determination of what qualifies as “work-related” can be nuanced. Under 29 CFR 1904.5, a condition is considered work-related if an event or exposure in the work environment either caused or contributed to the injury or illness. However, exceptions include activities like eating, commuting, or personal tasks unrelated to work duties.
Pitfall Example: A warehouse employee trips in the breakroom during their shift. Because the incident occurred on the employer’s premises and during work hours, it must be logged—even if it didn’t occur on the production floor.
How to Address It: Familiarize yourself with OSHA’s technical definitions and exceptions under 1904.5(b). When in doubt, document the incident provisionally and seek clarification to avoid accidental underreporting.
2. Not Tracking Restricted Workdays or Job Transfers
OSHA’s 1904.7(b)(3) requires employers to include any restricted workdays or job transfers resulting from an injury or illness. A common error is underestimating or omitting such cases, especially for injuries that result in temporary light-duty assignments.
Pitfall Example: A mechanic is temporarily assigned administrative tasks after sustaining a rotator cuff injury. If this assignment impacts their original job role (e.g., physical lifting), these restricted duty days must be accounted for in the OSHA 300 log.
How to Address It: Implement a flagging system in your internal records management to link medical restrictions to OSHA recordability criteria. Regular audits and consultations with your occupational health provider can help ensure no cases slip through the cracks.
3. Not Adhering to Privacy Protocols
Certain cases—such as injuries involving sexual harassment, mental health conditions, or infections like HIV, hepatitis, or tuberculosis—must be recorded in a way that protects employee privacy. Under 29 CFR 1904.29(b), these cases must be treated as “privacy concern cases,” and names should not be disclosed on the OSHA 300 log.
Pitfall Example: A mental health condition related to workplace stress is entered into the OSHA log with full employee details, violating privacy regulations.
How to Address It: Replace employee names with anonymous identifiers for privacy concern cases. Keep detailed records securely in separate, restricted files for internal reference.
4. Failing to Meet Electronic Reporting Requirements
Since updates to 1904.41, businesses in high-risk industries with 100 or more employees are required to submit OSHA 300 logs electronically through the Injury Tracking Application (ITA) annually. Missing deadlines or submitting incomplete data can result in penalties.
Pitfall Example: A manufacturing company submits its OSHA 300A form without verifying accuracy, only for discrepancies to emerge during an audit.
How to Address It: Pair your recordkeeping process with OSHA-compliant software to streamline electronic submissions and ensure adherence to e-filing deadlines. Schedule internal checks well in advance of OSHA’s March 2nd of the year after the calendar year covered by the form(s) (for example, by March 2, 2024, for the forms covering 2023) submission deadline.
5. Neglecting Mental Health and Ergonomic Cases
OSHA has increasingly emphasized capturing data on conditions like musculoskeletal disorders (MSDs) and mental health conditions caused by work-specific stressors. Many employers either miss or improperly classify these cases. Employers are expected to properly record cases that meet the criteria for a work-related illness or injury under 29 CFR 1904. This includes providing training to safety personnel and supervisors on recognizing the signs and symptoms of stress injuries, burnout, ergonomic risks, and mental health conditions that may be work-related. Conducting job hazard analyses (JHAs) to evaluate tasks for ergonomic risks and potential workplace stressors is also crucial for proactive prevention.
Pitfall Example: Employees suffer musculoskeletal pain due to repetitive motion or poor workstation ergonomics, but the company fails to log these injuries because they were initially classified as minor discomfort.
How to Address It: Train safety personnel and supervisors on recognizing signs of stress injuries, burnout, and ergonomic risks. Use job hazard analyses (JHAs) to evaluate tasks prone to repetitive motion injuries.
Advanced Strategies for Compliance
Embedding compliance into your organization’s culture is a great method for preventing costly errors. These advanced strategies can help elevate your safety management practices:
1. Conduct Root Cause Analyses on Incidents
Investigate each incident thoroughly. Identifying the root causes of accidents and near misses assists in implementing corrective actions and preventing recurrence. OSHA encourages trend analysis to uncover systemic issues. For instance, if slip-and-fall incidents are recurring, investigate potential causes like poor lighting, wet floors, or inadequate footwear.
2. Tighten Internal Definitions with Expert Guidance
Gray areas in incident recordability can cause inconsistencies. Consult with occupational safety consultants or legal experts to clarify definitions and align your protocols with OSHA standards. This reduces ambiguity and ensures consistent application of recordkeeping guidelines.
3. Audit and Update Processes Regularly
Safety regulations and best practices are constantly evolving. Schedule regular reviews of your safety management system, including recordkeeping processes, to identify gaps and address emerging risks. Incorporate the latest OSHA guidance and industry standards to stay ahead.
4. Prioritize Training Across All Levels
Safety is everyone’s responsibility. Provide targeted training for managers, supervisors, and employees on hazard recognition, safe work practices, and incident reporting. Empowering employees to identify and report hazards fosters a proactive safety culture and reduces risks.
5. Leverage Technology as a Safety Net
Modern safety software can strengthen your safety management. From incident reporting apps to training management and OSHA reporting integration, these tools enhance efficiency, accuracy, and accessibility. Technology ensures your safety processes are streamlined and compliant.
How to Stay Informed for 2025:
- Subscribe to OSHA’s email updates: The best way to stay informed is to subscribe to OSHA’s email alerts and news releases on their website.
- Regularly check the OSHA website: Make it a habit to visit osha.gov periodically to look for updates, news, and new publications.
- Follow OSHA on social media: OSHA often uses social media platforms to disseminate information.
- Consult with safety professionals: Safety consultants and legal experts specializing in OSHA compliance can help you stay abreast of the latest changes.
- Watch the recording of our webinar Advanced OSHA Recordkeeping: Avoid Costly Mistakes in 2025 with Dr. Scott Cherry and Matt Bearden from Sunstate.
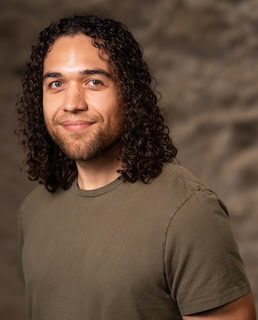
Cain Boney is a contributor to Axiom Medical’s blog. With a career dedicated to writing about the workplace, Cain focuses on how employee well-being affects organizational success and sustainability in the long term.